Developing Energy from Natural Wood Without Corrosive Chemicals
- 11 Oct 2017
- Volume 11
- NanoScientific Magazine, Fall 2017
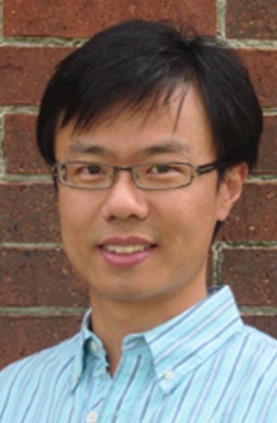
Phd Department Of Chemical & Biomolecular Engineering, The University Of Akron, Akron, Ohio Teexas
Dr. Jiahua Zhu is an Assistant Professor in the Department of Chemical & Biomolecular Engineering at the University of Akron. Dr. Zhu received his Ph.D. degree in Chemical Engineering from Lamar University in 2013 and received a Master degree in Chemical Engineering from Nanjing University of Technology (2009) and Bachelor degree in Applied Chemistry from Yangzhou University (2006). Dr. Zhu’s current research interest covers the fundamental study of multifunctional polymer- and carbon-based nanocomposites and explores their applications in emerging fields such as heat transport, energy storage, catalysis, environmental remediation, etc. Dr. Zhu has coauthored more than 100 peer-reviewed journal articles and three book chapters.His work has been cited more than 4,000 times with H index of 37. Dr. Zhu has actively served on TMS and AIChE societies as symposium organizer and session chair since 2011 and served as reviewer for more than 40 scientific journals. Dr. Zhu was awarded the Chinese Government Award for Outstanding Self-Financed Students Abroad, Young Leader Development Award from Functional Material Division of The Minerals, Metals & Materials Society, Early Career Award from Polymer Processing Society and Early Career Investigator Award from ECS Electrodeposition Division.
Feature Interview With Jiahua Jack Zhu Assistant Professor Chemical & Biomolecular Engineering
Please explain briefly how carbon is manufactured from natural wood and why it is a "greener" method?
The unique structured carbon is a replica of cellulose framework in the natural wood. Wood is like a building structure with steel frame (cellulose and hemicellulose) and concrete (lignin). By carbonizing the framework with a heat treatment process, the cellulose framework can be fixed as carbon framework. Then, lignin is selectively removed to left porous framework structure behind. Different from conventional physical and chemical activation processes, where corrosive chemicals or high-temperature process up to 800 oC are required to generate micropores, our method does not involve any chemicals. All that is needed is nitrogen, air, and a carefully programmed heating profile. By the combination of these three elements, the porous structure of carbon can be easily tuned without involving chemicals.
How does this process activate without corrosive chemicals?
The use of corrosive chemicals in traditional processes is to etch out micropores and enlarge surface area. It is very challenging to generate inter-connected pore channels. We developed a mild oxidation process that interconnected pore channels can be created by hot air. The principle is similar but the process is more economic and environmental friendly.
Can this process be used on other biomass resources?
This is a general method can be used for a great variety of biomass resources. So far, we have demonstrated the effectiveness of this method in processing softwood, hardwood, cotton and bamboo into mesoporous carbon and more testing is on the way.
How long will it be before this process is used in manufacturing?
We published our first research article in 2015 and immediately attracted industrial interests. A patent was filed (US 20160272502 A1) afterwards. Right now, we are working on the process optimization for better quality control of the porous carbon products. I would expect 2-3 years before it goes to manufacturing.
How are magnetic nano composites used to remove metal from polluted water?
The greatest advantage of magnetic nanocomposites is its high adsorption efficiency and easy recycling. A wellknown fact is that the smaller adsorbent usually comes with better adsorption capacity, while the separation and recycling of smaller adsorbent becomes more challenging. The magnetic nanoparticles embedded in bulk absorbent can attract toxic heavy metal ions or reduce them to less toxic forms. Meanwhile, magnetic nanoparticles enable fast separation by external magnetic field.
What are self organized Nano Crystals and why are they called the thermal highway?
Filler technology is widely adopted in the industry to produce thermally conductive materials. To reach satisfactory thermal conductivity, fillers need to be interconnected to cut off the thermal barrier between the particles. It can be done with extremely large fraction of fillers in matrix, however, the processability, materials cost and mechanical property of the composites will be sacrificed. Self-organized nanocrystals are thermal fillers that can be grown in polymer. The unique feature of this technology is to create interconnected crystal structure without interfaces. The phonon can be efficiently transported along the crystal structure without scattering. Therefore, such composite has great advantage in thermal conduction as compared to conventional composites.
How does Atomic Force Microscope help you image your research?
Since composites hold a promising future in the thermal management area and the interface is the major thermal barrier in composites, the focus of our research is to understand the thermal transport behavior across different filler/matrix interfaces. By using Scanning Thermal Microscopy technique on Atomic force microscope platform, we can clearly identify cylindrical structure by Park's new 3D AFM is having a huge impact on the performance of vertical devices such as FinFET, TFET, STT-MRAM and others.
Figure 1. (a) AFM three-dimensional topography of PVA/amino acid crystal composites, (b) corresponding scanning thermal images.