Nanoscale Characterization For The Oil & Gas Industry
- 30 Dec 2014
- Volume 3
- NanoScientific Magazine, Winter 2014
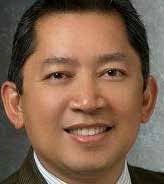
Dr. Rigoberto Advincula is Full Professor at the Dept. of Macromolecular Science and Engineering, Case Western Reserve University. He is also Associate Chair and Graduate Chair of the Department and Director of PETRO Case, a polymers for oil-gas consortium. He is Vice-Chair of the Polymer Chemistry Division (ACS) and previous President of the Philippine American Academy of Science and Engineering (PAASE). He is also Trustee with PhilDev Foundation.
He is Editor of Reactive and Functional Polymers and Associate Editor of Polymer Reviews. He has published more than 416 papers (H index = 42), 11 patents, and given more than 560 lectures and seminars. His area of research is in polymers, nanoscience, macromolecules, organic materials, hybrid materials, ultrathin films, polymers and additives for oil and gas, and corrosion: (1) synthesis of new functional nanomaterials capable of ordering at surfaces and interfaces, (2) application of surface sensitive spectroscopic, microscopic, optical, and electrochemical analytical techniques to understand ordering and phenomena, (3) devices and sensor applications of ultrathin films and particles, (4) biotechnology, (5) highly performance polymers and additives for fluids and coatings, and (6) sustainability engineering. He has been mostly been funded by the National Science Foundation, Welch Foundation, and several industry grants. He has had Visiting Professor positions at the Max Planck Institute for Polymer Research, Austrian Institute of Technology, Waseda University, McGill University, Tokyo University of Agriculture and Technology, and National University of Singapore.
He is also most passionate with training young minds in science and engineering careers. He has trained over 26 Ph.D. graduates, 50 undergraduates, and 40 high school students. A number have become successful Professors, R&D Managers, Ph.D. students, and many have won awards in their presentations at national meetings during their time in his group.
Dr. Rigoberto Advincula, Director of the Petro Case Consortium, is recognized industry-wide as an expert regarding polymer and materials challenges of the oil-gas industry. He is currently a Professor with the Department of Macromolecular Science and Engineering at Case Western Reserve University and is the recipient of numerous awards including Fellow of the American Chemical Society, Herman Mark Scholar Award of the Polymer Division, and Humboldt Fellow
How does the use of AFM (Atomic Force Microscope) help automate or improve the existing methods applied in oil & gas manufacturing?
AFM has many capabilities that SEM, TEM and optical microscopy does not which is surface forces and surface analysis - surface probe microscopy (SPM). It requires less sample preparation and the appropriate mode (multimode) can be chosen to focus on wetting, magnetic, friction, electrostatic behavior, etc. This is not easily probed in the other optical microscopy methods.
Is there a significant improvement in the manufacturing process for oil & gas that can be identified due to AFM and nanotechnology applications? What are they and how much is the improvement?
Right now, AFM is very much still in the academic area as far as oil & gas is concerned at least not to the extent that it is heavily used in the semiconductor industry. Typical manufacturing needs in the O&G industry concerns coatings, proppants, fluids, completion tools, elastomers, etc. AFM can first be useful in understanding the surface properties of these products but can be used a lot in failure analysis. It is a true nanoscale method as such the nanoscopic to microscopic phenomena can be probed as against macroscopic properties that are measured with existing industry standard testing from API, NACE, ISO, etc. This means that structure-property relationships can be greatly amplified.
Can you explain in detail the vast advantages of using AFM to understand phenomena on colloidssurfaces and predicting failures?
In surface and interfacial science which includes flat surfaces and colloidal surfaces, the SPM methods takes a very important tract since the surface forces that are susceptible to changes in wetting, shear, eletrostatic charging, morphology change and anisotropy - can be probed. In typical failure analysis this is often a "before and after" experiment or ex-situ. AFM has the capability to do in-situ or real time measurements of failure, e.g. with a temperature stage or a magnetic field. Also with AFM, it can be used with a nanoindenter (diamond) or even a spectroscopic method (Raman) to investigate specific fields or sample spots. Colloidal surfaces are accessible in dried or flat-pressed sample geometries.
Can you explain what failure analysis in materials means and why it helps to be able to provide analytics at the nanoscale level for oil & gas?
Failure is a series of events starting from the nanoscopic level all the way to microscopic. In oil & gas, high T, high P, and corrosive brine conditions can be investigated in terms of thermodynamic and kinetic considerations. The failure at the nanoscopic level can involve a series of bond-breaking events or field driven changes in anisotropy or crystallinity. This means that a first principle explanation is based on a chemical reaction or physical desorption or delamination at the nanoscale level. The same also applies to deposition (as in scaling and other petrochemica or microbiall fouling mechanisms).
Currently, the Oil & Gas Industry looks up to Nanotechnology to ensure optimum performance of chemical interfaces during production using AFM in numerous applications to ensure the highest degree of efficiency in manufacturing. Can you explain how AFM increases efficiency in oil & gas manufacturing?
AFM allows exposure and understanding of the mechanisms of failure or the promise of a strong structure-property correlation. By understanding first principles or distinguishing first vs second order transitions and phase separation, one is able to improve on the design of the synthesis or the formulation of the material or fluid. The performance of a product is only as good as control of the weakest point or link - or a rate determining step.
Please describe in some detail the way that AFM characterization is an improvement to the old method of inspection and how it improves production yield, saves money, automates the process, etc. What are the benefits?
AFM should be compared in terms of what is normally used in the industry with SEM, TEM, and optical microscopy. As mentioned, AFM is not just an imaging technique but an in-situ and interactive method that includes more experimental design as a probe. In a way, AFM can answer many questions that would have taken 2-4 additional analysis methods. If not AFM complements a lot of what you get from the other microscopy methods. The field is wide open for exploring the many different number of modes ( non-contact, phase imaging, elstrostatic force, frictional force, magnetic AC, etc. that can be paired or augment any existing industry standards testing in the macroscopic realm.
What future improvements might soon be available to the oil & gas industry in the field of Nanotechnology and AFM inspection and will they significantly enhance or improve the processes?
This could involve the use of AFM for high throughput analysis of failure or high throughput screening of new materials. Another is that the AFM method could further be hyphenated with other experiments, e.g. combine with spectroscopy, magnetic field, electrochemistry, etc. AFM is able to complete the picture from other spectroscopic, microscopic methods and could one day be a routine analytical method, accessible to a growing number of scientists and engineers.